Powder coating preparation
Replace the Zinc Phosphate system with Picklex® 20 Process at Room/Ambient temperature, No Re-cycling for Powder coating, with Zero Waste Disposal …
Complete Surface Preparation & Pre-treatment (Conversion coating) in One Step. Provides 100% Clean surface & stops further oxidation before Finishing...
Eliminate Sanding, Blasting, Acid, Phosphate, Chromate etc. for all Ferrous & Non-ferrous metals including Hot Rolled steel with mill scale
Comparison of Traditional Zinc Phosphate system with Picklex® Process before Powder coating
Traditional Process:
With Zinc
Phosphate system
Rinsing
Rinsing
Acid Pickling
Rinsing
Rinsing
Activation
Zinc Phosphate
Rinsing
Sealer Rinse
Oven Drying
Powder coating
Picklex® 20
No blasting is needed for New Metal. Mill scale does not have to be removed from Hot Rolled Steel
Picklex® 20 is used at Room/Ambient temperature. Not Re-cycled:
- Picklex® 20 Process with Rinsing & Oven Drying (Manual or Automated):
- Picklex® 20 spray as Heavy Mist
- Rinse with regular Tap water (for Manual process). Rinse water is not a Hazardous Waste
- Rinse (second rinse for Automated process)
- Oven Dry
- Powder Coat
- Picklex® 20 Process without Rinsing & Oven Drying (Manual process):
- Picklex® 20 spray as Heavy Mist
- Blow off the excess Picklex® 20 completely from the metal surface to avoid having any Residue
- Air Dry (allow few hours for complete drying)
- Powder Coat
Note: The Picklex® 20 coated parts will not Rust for several years, if kept Indoors under any Humidity condition before Powder Coating
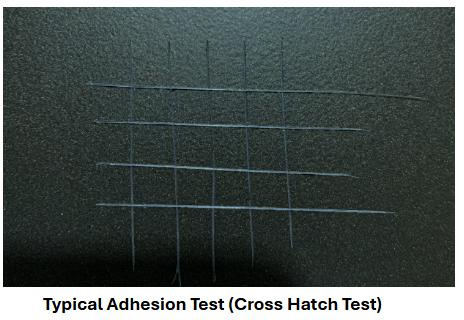
NOTE: For large Spraying or Dipping 3-Step System (Re-cycled), see Picklex® Process
Complete Surface preparation/Pre-treatment of Flash rusted steel
— US EPA Tested/Verified, National Award & Edison Award winner
Performs Complete Surface preparation & Pre-treatment in One Step as follows:
- Removes light mill oil, cutting fluid, surface rust
- Provides a nano-thickness conversion coating
- Completely coverts 100% Mill scale, Pitted Rust, Weld/Laser scale to a Paintable Conversion coating …
- Seal the coating and stop further oxidation until it is Powder coated (including High Temperature Paint/coating)
Benefits:
- Complete Green Process
- Eliminates Sanding, Blasting, Acid, Phosphate, Chromate etc. presently used in the metal surface preparation process
- Mill scale does not have to be removed from Hot Rolled Steel
- Zero Waste Disposal
- No sludge
- Rinse water is not a Hazardous waste
- No down time
- Provides a rust/contamination free surface with Zero oxidation
- Does not etch the metal surface, so the surface stays intact
- Provides years of indoor Rust protection without top coating
- High Temperature Paint/coating can be used
- No EPA or OSHA regulation
- Passed over 1500 hours of Salt Spray Test (ASTM B117)
Benefits
Presented at National Hot Rod Magazine show in Huntsville, AL. April 1999
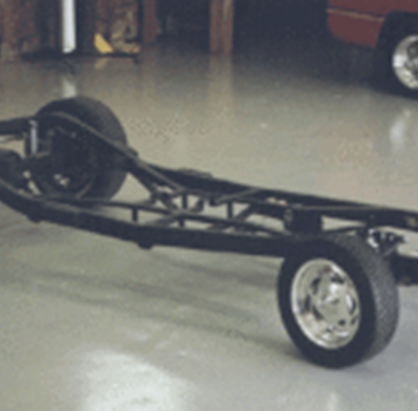
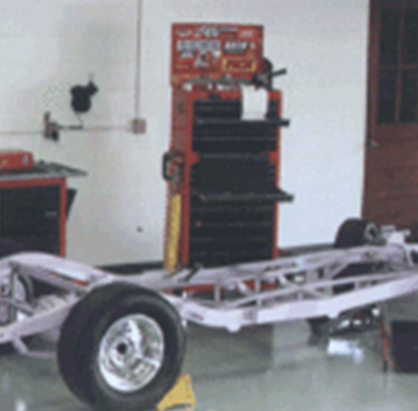